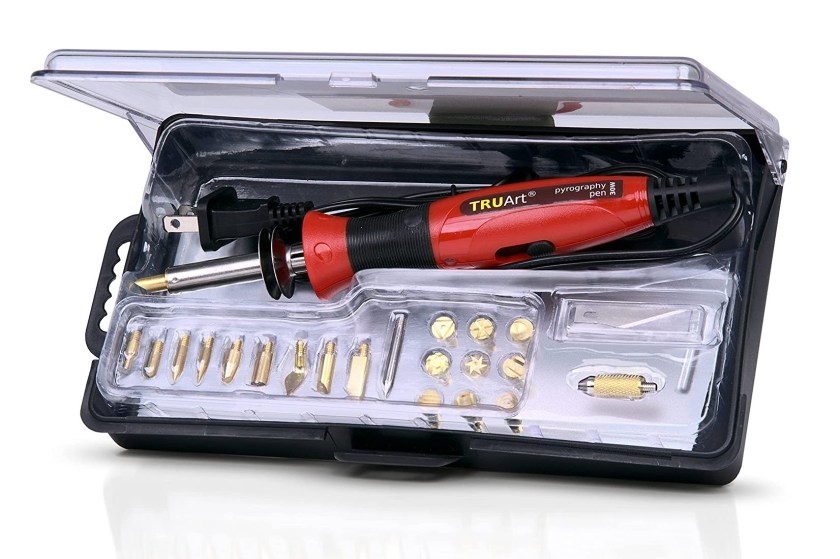
There are many materials available to make wood burning art. Basswood, for example, is a great choice if your goal is to achieve a clean color with no visible grains. Unfortunately, this wood is often very expensive and hard to find in the size you need. Birch wood, another popular material, has a fine texture with a bright color and no differences in the annual growth rings.
Preparing wood to be used in pyrography
Preparing the wood for pyrography is the first step. Dark wood does not show the art very well, and a pronounced grain pattern will make the art hard to work with. For pyrography, it is a bad idea to use resinous woods or uneven timber. Make sure to clean the wood before you start burning it. Once the wood is prepared, you can start burning it!
Although shellac can be used for pyrography projects sealing, it is temporary. Shellac causes wood to discolor when it is exposed to heat and should not therefore be used on cutting boards nor coasters. Paste wax is an alternative to shellac. Paste wax gives wood a smooth, natural sheen when it is applied. It is also simple to apply and looks natural.
Wooden design.
If you want to add design to your wood burning art, start by creating a light sketch of the design that you'd like to create. You can use a pencil, eraser or ruler to create the design. Pre-made stencils prove to be particularly helpful. For beginners, you can purchase complete wood burning sets. Below are some wood burning design suggestions to get you started.
You can also paint on the burned art. You can use a pointed pen or a flat one. Be careful to not burn too deep or you will end up with holes in the work. In addition to painting, you can add shading to your wood burning art. You can color it once you're done. After the wood has cooled you can add shading.
Creating Lichtenberg burns
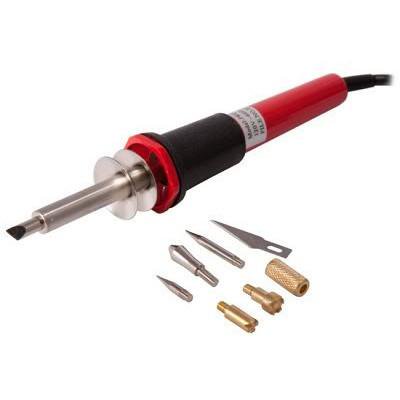
Creating Lichtenberg burns is an art form with a lot of potential. Branching electrical discharges can be created by using a microwave converter and a high-voltage source. Lichtenberg first discovered Lichtenberg figures in 1777. Lichtenberg's wood burning is becoming a more popular form of art thanks to fractal wood burning. These are the steps to creating these figures.
Before you begin, you'll need some safety equipment. The majority of high-voltage transformers used to power appliances or neon signs are high-voltage. These transformers have a higher chance of electrocution due to their vulnerability to live wires and unprotected. You also need to wear gloves and be careful when using a Lichtenberg device. A pair of rubber gloves is also recommended. When using gloves, you should only touch one side of your hand, keeping the other hand behind your head. Although you may still get electrocuted if your hands come in contact with an energized electrode it won't stop your heartbeat. You should always bring someone with you when using a Lichtenberg tool. The second person can turn off electricity in the event you become electrocuted.
You first need to have a power source. A high-voltage, electrical source is required to power a Lichtenberg device. To burn wood safely, the electrical current must not exceed 2,000 volts. This is why the majority of woodworking groups forbid this technique. Safety is the main concern, regardless of whether you are creating a Lichtenberg figure. When working with electricity, always wear gloves and protective clothing. Also, double-check your electrical outlet before you make contact.
Use a stencil
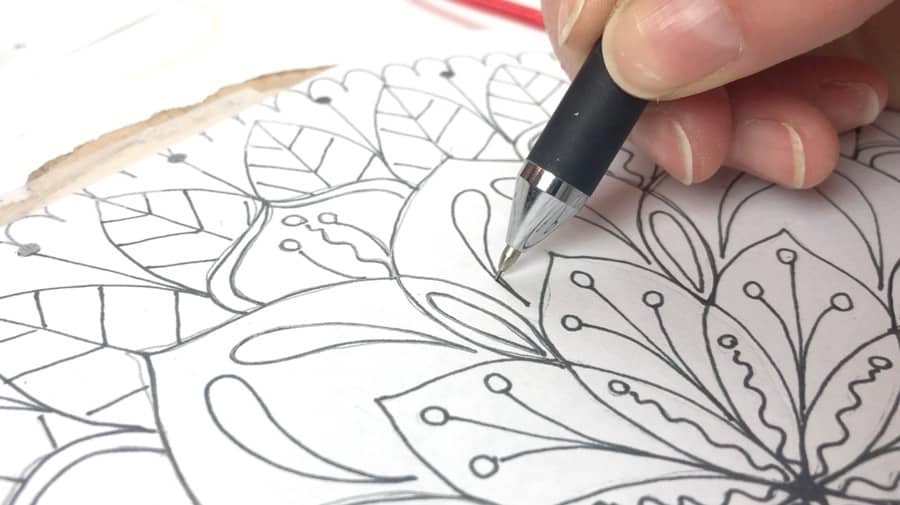
If you are looking to create intricate wood-burning designs, a stencil is an ideal tool. A stencil can be used to trace a design onto graphite sheets and then transfer it to the wood. The stencil will serve as a guide for your hands and eyes, but the final design is entirely up to you. It is okay to use a pencil when drawing a pattern. However, it is dangerous to simultaneously hold the stencil in your hands and the wood.
First, sand your wood so that you can burn the image. After you have sanded your wood, you can start working on the design. You will need to apply some pressure to transfer graphite onto the wood to make sure that the design is clear. After you're done, take out the tracing paper.
FAQ
What types of woods are best for furniture making?
Woods are classified by their hardness. Softwoods are pine, cedar and cypress. They're often used for outdoor furniture because they don't rot easily. Hardwoods include oak, maple, mahogany, and teak. They can't withstand the elements outside so they're best kept indoors.
What material would your recommendation be to learn woodworking?
You can start with softwoods like pine or poplar. Once you feel comfortable with these two, move on to hardwood.
How can I organize my shop?
Setting aside an area to store tools is the first step in keeping your workshop organized. You want your tools to stay clean and free from debris and dust. To hang accessories and tools, use pegboard hooks.
How do I determine what kind of wood my project is made from?
Always check the label before purchasing wood. It should have information about the wood species as well its moisture content and whether any preservatives were used.
How much money does a hobbyist have to put into getting started?
To start your own woodworking company, you will likely need capital to purchase the necessary tools and other supplies. Start by getting a small circular saw saw, drill press or circular saw. These items aren’t too expensive so you won’t have to break the bank.
Where to Buy Hardwood Lumber?
Home Depot sells hardwood lumber. You will find a range of wood products available at Home Depot.
There is also a wide selection of engineered hardwoods, including Ipe (Araucaria Angustifolia), Brazilian Cherry(Pau d'Arco), Mahogany (Swietenia Mcrophylla).
These woods can be found online by searching for "hardwood lumber" in Google.
Statistics
- Most woodworkers agree that lumber moisture needs to be under 10% for building furniture. (woodandshop.com)
- The U.S. Bureau of Labor Statistics (BLS) estimates that the number of jobs for woodworkers will decline by 4% between 2019 and 2029. (indeed.com)
- If your lumber isn't as dry as you would like when you purchase it (over 22% in Glen Huey's opinion…probably over 10-15% in my opinion), then it's a good idea to let it acclimate to your workshop for a couple of weeks. (woodandshop.com)
- The best-paid 10 percent make $76,000, while the lowest-paid 10 percent make $34,000. (zippia.com)
External Links
How To
How to stain wooden surfaces
The process of staining wood involves the application of chemicals to the wood's surface, which causes it to change its color. This chemical reaction causes wood to turn from whiteish to brownish. The most common type of wood used for staining is oak, although many other types of wood can be stained.
There are several ways to apply stains to wood surfaces. Some methods involve mixing the stain with a solvent (such as turpentine) and then brushing or spraying the mixture onto the wood. You can also apply a solution containing water and dye directly to the wooden surface. You can also mix stains with varnishes or paints so that they become part the finish coating.
Preparing the surface is the most important step in staining wooden surfaces. The wood must be thoroughly cleaned to remove all grease and dirt. Sanding the wood removes scratches and imperfections. Next, you need to decide which stain you want. There are two main kinds of stains available: non-penetrating stains and penetrating. Penetrating stains penetrate deeper than non-penetrating stains, which makes them great for dark colors like mahogany. Light colors such as maple work well with non-penetrating stain.
After deciding on the type of stain, you want to apply, prepare your tools. You can use a paintbrush to apply stains. This allows you spread the liquid evenly over the surface. To remove any stains left behind after painting, you will need some rags. If you are planning to mix your stain, ensure you have enough containers for each component.
Once you have prepared all your materials, it is time to clean the areas where you will stain the wood. To remove dirt and dust, use warm water and soap. Wipe the entire piece of furniture with a rag dampened with clean water. You should remove any debris, especially if your plan is to stain darker wood.
Next, apply the stain. The stain can be applied by spraying or brushing the stain onto one end of the furniture. Slowly and carefully work your way along the grain to reach the opposite end. Keep the stain from dripping off the wood's surface. Allow the stain to dry completely before you move on to the next step.
Clear polyurethane is used to protect the painted surfaces. Apply three coats of polyurethane sealer. Let the third coat dry overnight before you sand the final coat.