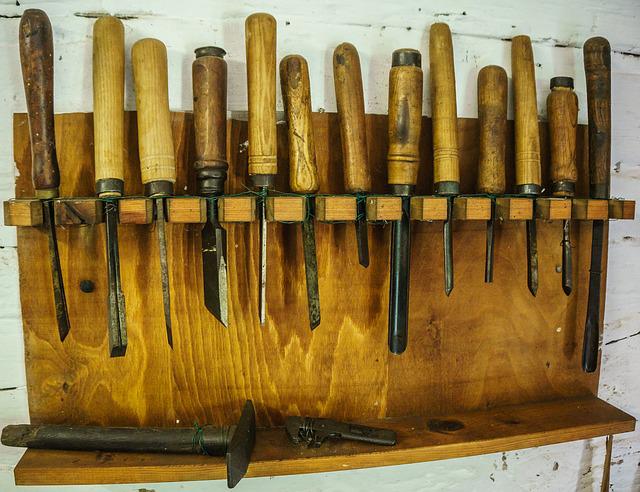
Philip Moulthrop first started turning wood in 1978, after his father Ed Moulthrop taught him the craft. Using a hand-forged lathe and chain saw, he roughs out the green sections of trees from southeastern regions. After he finishes the bowl of the lathe, he refines it and then adds several coats of finishing. The entire process can take from four months up to one year. The bowls can be bought or given as gifts once they are completed.
Philip Moulthrop
The Phillip Moulthrop bowl is a stunning red leopard maple vessel. Wood turning, which he invented, is a family tradition that has been passed down through three generations. Philip Moulthrop’s bowls are not only their own creations but also part of several prominent museums' and private collections all over the globe. Here are some of their most popular pieces. You can read more about this talented artist by reading the following.
Born in 1947, American artist Philip Moulthrop. He was a student of general arts during his early 20s. However, he developed a keen interest in woodworking and a love for it later on. At age 16, he bought his first lathe and gradually expanded his equipment. He created beautiful, turned vessels which attracted the attention and support of the arts community as well as the president of the United States. His work was quickly recognized, and he began selling his items at local craft fairs.
Matt Moulthrop
The Matt Moulthrop bowls are a wonderful example of Georgia's rich woodturning tradition. The artist was born and raised in Atlanta. He received his BA from Georgia Tech and MBA from Georgia Tech. While he did spend a few years in the 9-to-5 industry, he never lost passion for turning wood. He won national recognition for his bowls. His work is on display at ASU Art Museum, Carter Center, and Racine Art Museum.
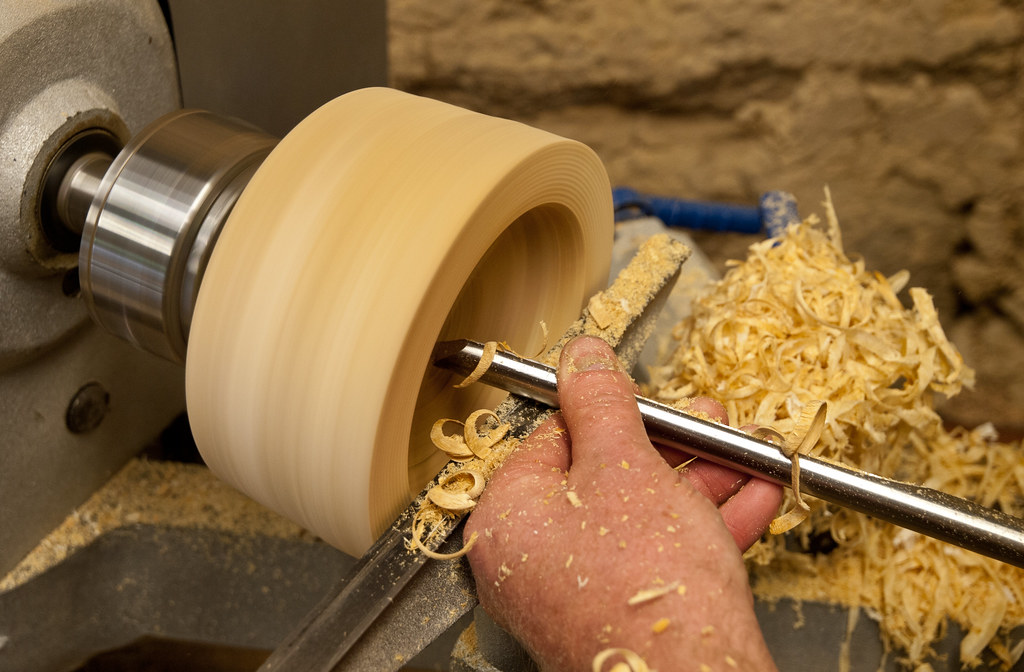
The Moulthrops were recognized as world-class woodturners. Their works have been placed in prominent collections across the United States and around the globe. Moulthrop's own pieces are held in the Renwick Gallery of the National Museum of American Art. His bowls are collected by collectors worldwide. During a Smithsonian photo shoot, the bowl maker gave each photographer a signed copy.
Ed Moulthrop
Moulthrop began making bowls in the 1970s. He soon received a scholarship from Princeton University to study architecture. Moulthrop quit architecture to become a woodturner after spending a year living in Vietnam. His large-scale, turned bowls are internationally recognized and can be found in museums like the Museum of Arts and Design in New York and the White House Collection of American Crafts. These bowls have a clear, polished finish and are made of domestic woods.
The rare Ed Moulthrop bowl measures nine inches across by fourteen inches and is made from wild cherry. These wood bowls may be purchased at Gump’s in San Francisco. There are many other pieces of Ed Moulthrop's wooden bowls on display. Visit the exhibition to get a better idea of his work. He also produces a beautiful catalog of his work. You can buy his bowls in museums but it is better to go to his studio and actually see it.
The Eagle & Phenix Dam Series
This limited edition collection of moulthrop bows uses wood from Eagle & Phenix Dam. The dam was built in Columbus, Georgia. The bowls have historical traces and were handcrafted in Atlanta by Philip and Matt Moulthrop. They are available to bid during regular museum hours. Additionally, a portion will be offered for sale live.
The Moulthrop families has played a significant role in Georgia's development of wood-turned bowls. Three generations of Moulthrop families have been turning bowls over fifty years. The museum is proud of their works. Many of these pieces are prized due to their large size and smooth, polished surface. The exhibit also showcases his unique mosaic bowl technique which uses glue and thin branch to attach to a turned container.
Matt Moulthrop’s work
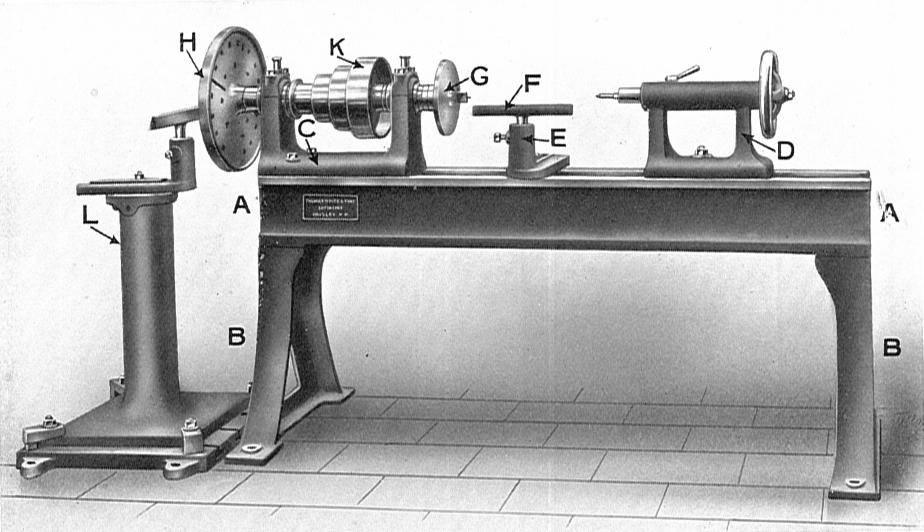
Matt Moulthrop was the son of Philip Moulthrop. His father was a pioneer in woodturning, and he continued to love it. Matt started his woodworking career after completing his BA degree at the University of Georgia. He also completed his MBA at Georgia Tech. He is now the third generation who makes wooden vessels. His work has been featured in numerous prominent art institutions, such as the ASU Art Museum (now the Carter Center). He is currently working on commemorative pieces for the Georgia Tech Alumni Association's 100th anniversary.
Georgia is not home to the wood he turns. To find unique wood, he travels all over the globe. He creates unique pieces by turning trees from around the globe with tools and a hand-forged, lathe. His pieces include wood harvested from trees that have fallen in the Southeast as also exotic locations such as volcanoes, underwater forests, and other places. If you are a fan of his work, be sure to check it out!
FAQ
Which woods are good to use for furniture-making?
Woods can be classified according to how hard they are. Softwoods include cedar and pine as well as cedar and cedar. They're often used for outdoor furniture because they don't rot easily. These hardwoods include maple, mahogany and teak. They are generally indoors as they don't weather well outside.
Do I have the potential to make a decent living doing this?
Yes! In fact, many woodworkers already do. According to the U.S. Bureau of Labor Statistics' (BLS), in May 2012 the median annual wage of woodworkers was $34,000 This is higher than the $31,000 annual national average.
Does it take a genius to make woodworking work?
No. Woodworking does not require any special skills. Anyone can learn how to use basic power tools and techniques to create beautiful works of art.
How can I keep my shop organised?
Setting aside an area to store tools is the first step in keeping your workshop organized. Keep your tools away from dust and debris, so they stay sharp and ready to work. Hang tools and accessories using pegboard hooks.
What is the minimum investment a hobbyist needs to make in order to get started?
A lot of capital is required to purchase the necessary supplies and tools if you want to start your own woodworking shop. Start by getting a small circular saw saw, drill press or circular saw. These items don't cost much so they won't break your budget.
What tools should you start with to become a woodworker
Woodworking is an art. It requires patience. It takes time to learn how to use all the different tools and techniques required for woodworking.
There are many options for woodworking equipment today. Some people prefer to use power tools while others prefer manual tools.
While you have the option to pick what you like, it is essential that you get the right tool for the job. It may be a good idea to start with a basic set, if possible, if you don’t know much about hand tools.
You could also try learning how to use a router which is used to cut intricate shapes into wood. These tools can be purchased at most hardware stores.
Statistics
- Average lumber prices rose about 600 percent between April 2020 and May 2021. (familyhandyman.com)
- In 2014, there were just over 237,000 jobs for all woodworkers, with other wood product manufacturing employing 23 percent; wood kitchen cabinets and countertop manufacturing employing 21 percent. (theartcareerproject.com)
- The best-paid 10 percent make $76,000, while the lowest-paid 10 percent make $34,000. (zippia.com)
- Most woodworkers agree that lumber moisture needs to be under 10% for building furniture. (woodandshop.com)
External Links
How To
How to properly operate a handsaw
Hand saws are used to cut the wood into pieces. The most common types of hand saws are circular saws, jigsaws, table saws, band saws, saber saws, crosscut saws, miter saws, and rip saws. A hand saw is made from metal or plastic and cuts materials such as wood, plastics and metals.
Hand saws have the main advantage of cutting at precise angles without needing to adjust the blade. It's also much easier to sharpen them than power tools. There are also some drawbacks. These devices are bulky and heavy so you need to be careful when transporting. You could also injure your self if you don't know how to use them.
There are many ways to hold a handheld saw. While cutting, keep your fingers away from the blades. If you don't, you might get hurt. While holding the saw, make sure you place your fingers around its handle. Keep your thumb close to the blade. This way, you won't accidentally touch the blade.
Never place anything under a piece of wood that you're cutting with a handsaw. Doing this would cause the blade to slip off the wood's surface. Before you start cutting, ensure that you inspect the area. Check for nails, screws and other objects underneath the wood.
Safety goggles should be worn when using a handsaw. They prevent dust from getting into your eyes, making it easier to see what you're doing. Safety glasses also protect your eyes from flying debris.
Before you start working with a saw, it is important to learn how to use it safely. Next, practice until your confidence is high enough to begin cutting. Once you know the basics, it will be easy to cut anything.