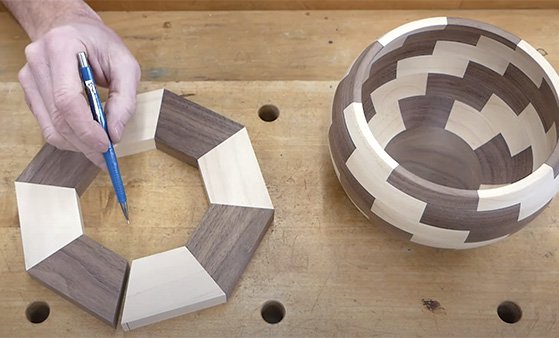
Patented Negative Rake Carbide Cutters are a game changer in the woodworking world. These cutters allow for safer and smoother cutting, which makes it possible to transform super-hard woods as well as man-made materials without having to sand. Also, smooth cuts mean that the job is completed in a shorter time. Negative-rake cutters are safer than traditional carbide ones and are much easier to use.
Cutting forces can be reduced with positive rake carbide cutters
Positive rake angles in carbide cutters are more effective at reducing cutting forces. They can reduce chip load and sustain higher cutting forces. This type of cutter is also more capable at chip-reduction, as the positive rake cutting edges have a thicker blade than the counterpart. However, the chip reduction ability of positiverake carbide cutters is only a qualitative indicator. It depends on other factors including the wedge's strength and thickness. The more thin wedges associated with positive-rake are more susceptible to chip loading and machine vibration. Impact loading can cause the wedge to break down, which can lead to poor productivity.
The relative orientation between the cutting face and the work is known as the rake angle. There are two types of rake angles. Positive rake means that the angle of the rake is less than 90 degrees. The negative rake carbide cutter is characterized by a blunter cutting edge and a less sharp rake. Both positive rake and negative rake carbide cutters have their pros and cons.
Negative rake carbide cutters produce better cuts
If you want to make a smooth and safe cut, then you will definitely benefit from using negative rake carbide cutters. These tools will help you to turn hard woods and other manmade materials. They will reduce chipping and catching and will make your work much easier. These cutters can also be used for a very long time. A Negative Rake Carbide cutter will last approximately 80 hours of continuous turning.
Easy Wood Tools invented and developed the negative rake carbonide cutter. This cutter is better at cutting acrylics and hard woods, while offering a longer life expectancy. These cutters are also equipped with a 4-inch countersunk machine screw. This type of carbide cutter also has the optimal three G's of Carbide. They are a great investment for your woodworking project.
TiN carbide cutters reduce cutting forces
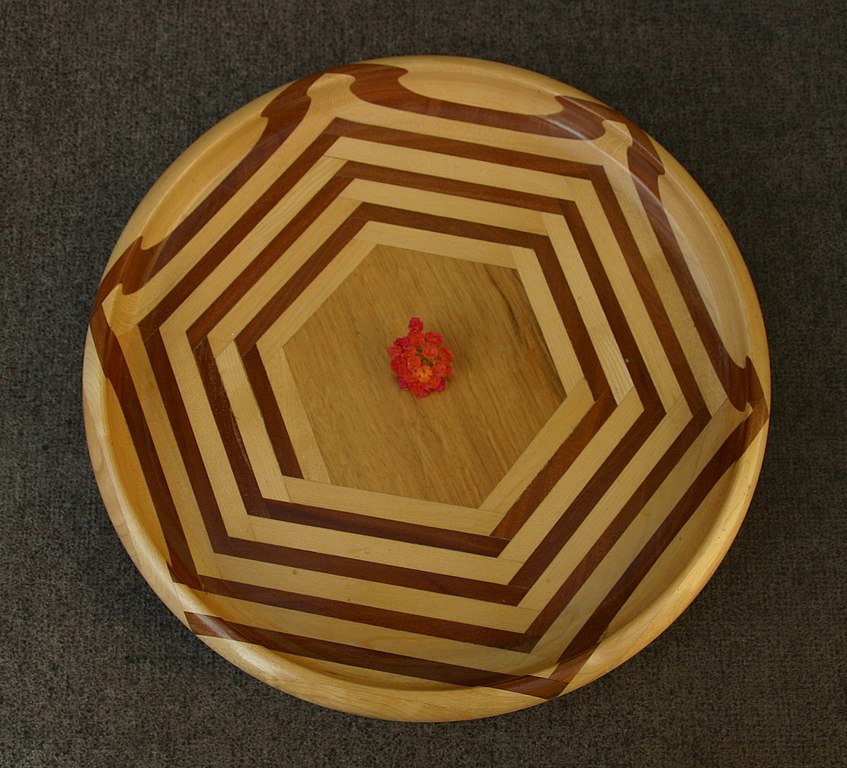
TiN carbide cutting tools produce lower cutting forces than standard tools. However, cutting speeds are not directly related to the cutting force generated by TiN carbide cutters. The process parameters such as cutting speed and signal-to-noise (SNR), have a greater impact on the cutting force. A model was developed to calculate this signal-to-noise ratio. This model can be used to determine the impact of cutting parameters.
Two types of carbide tools were used to study the cutting force: one was made from uncoated carbide, the other with Titanium Nitride's (TiN), coating. They measured flank and crater wear using optical microscopy and machine vision systems, and cutting forces were monitored using a dynamometer. The TiAlN-coated carbide tool showed the best response to cutting forces.
Experiments have shown that the temperature of TiN-coated, tungsten carbide cutters is affected by different cutting parameters. The temperature of Line I increases gradually at 280360 m/min, while the temperature of Line J and Line K rises rapidly at 320440 m/min. This improvement in feed per tooth was responsible for the increase in cutting temperature in the TiAlN-coated tools.
Authentic Easy Wood Tool - Negative Rake Caride Cutters
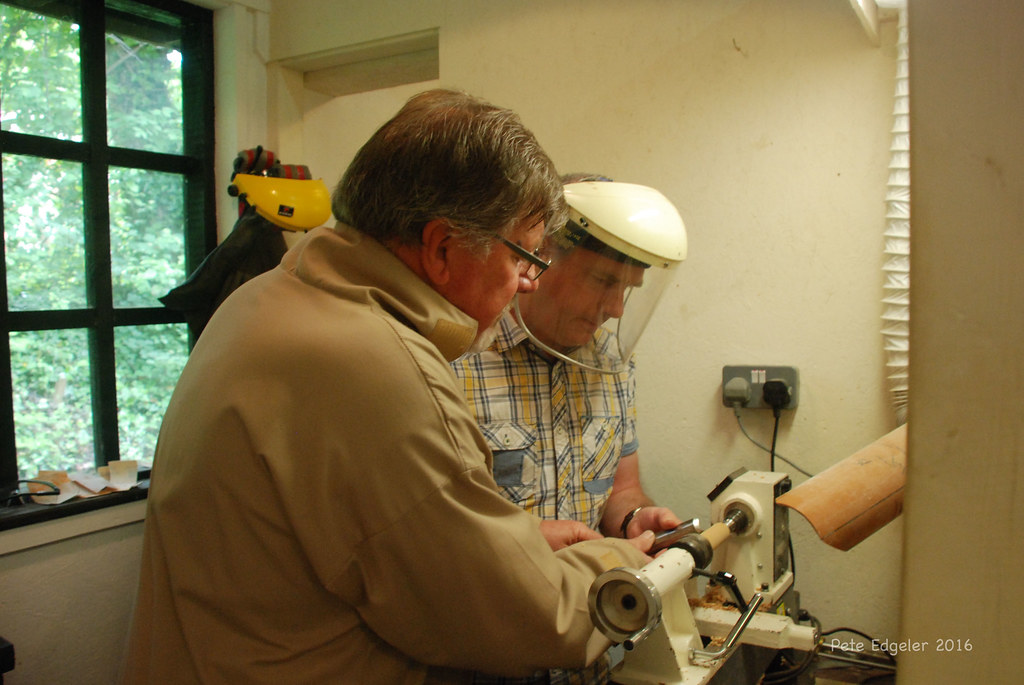
One of the top choices for quality cutters is the Authentic Simple Wood Tools Negative Rake Carbide Cutter. These tools are made in the USA and can be used with the Easy Wood Tools Mini, Pro Size Roughers, and Micro Detailers. Negative rake carbide cutters provide a smoother finish with fewer "grabs" and are made with the best grade of carbide to ensure maximum performance and durability.
Easy Wood Tools' carbide cutters reduce chipping, catches and other problems when working with man-made material. These cutters reduce chipping, sharpening is unnecessary, and they provide a very smooth finish. The carbide cutting edge is held directly below the workpiece. This transfers the pressure down to the wood. Easy Wood Tools' negative rake carbide cutters work well for woodturning projects.
FAQ
What tools work best for me?
It's important to consider your preferences and needs when buying tools. Are you more comfortable with plastic or metal handles? What size screws and nails do you use most often? Do you prefer hand tools over power tools?
Where can I purchase woodworking supplies
There are many places you can get everything you need, and you don't have to go far. You could also visit hardware stores in your area or shop online at Amazon.com.
You might also consider flea markets and garage sale for any old furniture or other materials you could reuse.
What kind of wood should you use?
The most commonly used woods for woodworking are oak, maple, cherry. Each wood variety has distinct characteristics that influence the final product's look and feel. For example, oak tends to be darker and harder than other woods. Birch is lightweight and soft while mahogany is heavier and denser. You also have the option of solid wood or veneers. Veneers consist of thin sheets made from wood and glued together to form a single layer.
How do you calculate woodworking prices?
Remember to keep costs as low as you can when calculating project costs. Always ensure you are getting the best possible price for materials. It's also worth taking into account all the other factors that may affect the cost of your projects, such as time, skill level, and experience. If you want to get an idea of what you can expect to spend on different types of woodwork projects, check out our guide to the average price of common household DIY tasks.
You can learn how to woodwork.
The best way to learn anything is by doing. Woodworking is an art form that requires patience, practice, skill, and experience. To master any craft, it takes time.
The best way to learn how to do something is actually to do it. Start small and learn from your mistakes.
What is the difference between a hobbyist woodworker and a professional woodworker.
Hobbyists enjoy making things out of wood, whereas professionals focus more on the quality of their work. Hobbyists usually take pride in their creations and often share them with friends and family. Professionals will spend hours looking at designs before they start to build a project. Professionals will be meticulous about all aspects of their work, from selecting the right materials to finishing it.
Statistics
- The U.S. Bureau of Labor Statistics (BLS) estimates that the number of jobs for woodworkers will decline by 4% between 2019 and 2029. (indeed.com)
- Overall employment of woodworkers is projected to grow 8 percent from 2020 to 2030, about as fast as the average for all occupations. (bls.gov)
- If your lumber isn't as dry as you would like when you purchase it (over 22% in Glen Huey's opinion…probably over 10-15% in my opinion), then it's a good idea to let it acclimate to your workshop for a couple of weeks. (woodandshop.com)
- The best-paid 10 percent make $76,000, while the lowest-paid 10 percent make $34,000. (zippia.com)
External Links
How To
How to make wood joints
This tutorial will help you join two pieces of wooden together. We will use the pocket hole joint, which is drilling holes in the wood to join them. If your wood has a straight grain, smooth surface, you can use this method. You may want to consider other methods, such as dowel joining. These are the steps
-
Drill Pocket Hole Joints. Start by measuring and marking the spot where the pocket hole joint will be placed. You will then drill 3/4" deep holes through each piece of wood with a jigsaw, handheld drilling machine, or hand-held drill.
-
Sand Smooth. Sanding the wood's edges will help ensure that the joint won't split later.
-
Glue together. Apply glue on both sides of the wooden plank. Allow it to cool for at least 5 minutes before you attach the pieces.
-
Attach the Pieces together. After the glue has dried completely, you can clamp the pieces together until they are flush.
-
Trim Joinery. Trim the excess wood around the joint after the glue has dried completely.
Be sure to leave enough space between each piece so that they can be turned inside-out.